Bracket-based Assemblies: Balance and Performance
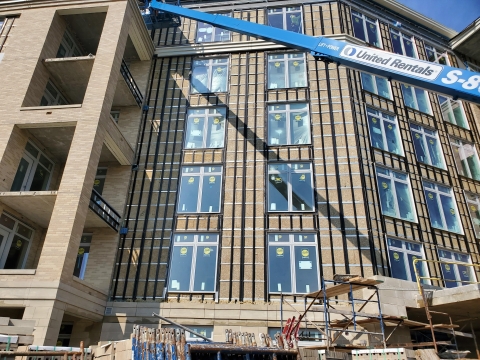
As rainscreen cladding took hold in the US design market, Z girts have proven to be challenging to seal for water/airtightness and are very inefficient thermally. Although commonly utilized due largely to budgetary constraints, the structural and load challenges, thermal inefficiencies, unnecessary breaches to the weather barrier, and fundamental installation inefficiencies of the Z girt approach are increasingly dating and disproving this approach for long-term rainscreen assembly performance.
Additionally, there is increasing evidence and data to illustrate that the Z girt approach, although deemed simple and cost-effective, actually is fraught with hidden costs and performance risks that can be easily negated by selecting an engineered, bracket-based wall assembly approach.
In contrast, a bracket-based system for rainscreen cladding should meet a balance of properties to provide long-term high-performance walls:
- Punched holes in brackets to allow for sealant of screw penetration of the air barrier. Dipping the screw threads or buttering the hole prior to screwing will provide a very effective seal at the penetration of the membrane.
- Internal shimming – by punching a “thumb” or “helping hand” into the bracket you can build into the system 1 ½” of adjustability to plane out the cladding and eliminate any of the complicated, time-consuming, and poorly sealed shims behind the Z girts.
- Variable bracket legs to accommodate any cavity depth from 2” to 11” deep systems.
- Thermally broken and thermal modeling provided in each design to meet the energy code requirements for opaque walls.
- High strength to weight ratios allowing for maximum spans or spacing of the brackets to minimize thermal bridging. Also, high corrosion and fire resistance contribute to the 50 to 100-year design life of these assemblies. Aluminum or stainless steel are ideal metals for selection, not compromised by corrosion of holes common to galvanized metal or fire in the case of FRP plastic girts or brackets.
- Fully-engineered assemblies with integrated shop drawings coordinated with the cladding material specific to the project that meets all the wind load, dead load, and deflection criteria of the panel and coordinated with the panel shop drawings to handle all the thermal and slab edge deflection criteria.
A holistic approach to complex code requirements and wall assemblies are the best solution to sound engineering and sound design. Before we can address a holistic design, we must understand the multitude of performance requirements in our complex, demanding assemblies today. With over 25 years of demonstrated, real-life experience in the North American rainscreen market, the ECO Cladding wall bracket, and rail assemblies effectively address all the performance problems outlined above and should be considered for all types of rainscreen cladding design assemblies.
Interested in learning more? Contact our technical team and we can provide you with a White Paper on this topic.